Building Safer Workplace Environments: Using Nudge Theory for Better Hand Safety in India
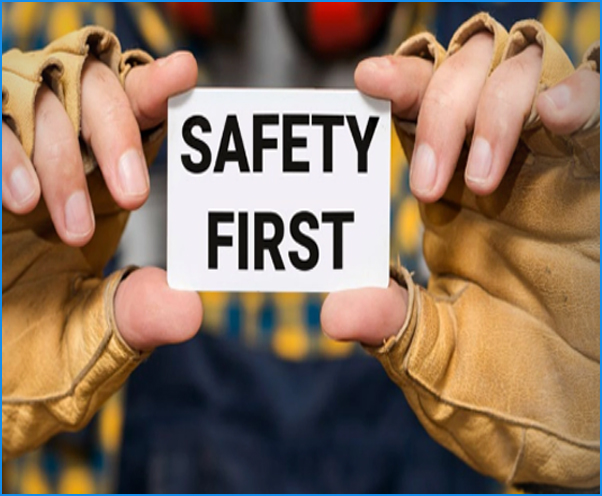
Highlight:
Nudge theory, a behavioral science approach, can improve hand safety in Indian workplaces by encouraging safer practices through gentle cues. By redesigning tools, enhancing training, and fostering awareness, employers can reduce injuries and build safer, more efficient environments where safety becomes an ingrained habit rather than an obligation.
In India, workplace safety is a pressing issue, particularly in industries like manufacturing, construction, and agriculture, where hand injuries account for a significant portion of workplace accidents. Despite regulations and safety protocols, many workers continue to engage in unsafe practices, leading to avoidable injuries and losses for both employees and employers.
One innovative solution to address this problem is nudge theory, a behavioral science approach that influences decision-making through subtle, indirect interventions. Unlike traditional methods that rely on penalties or mandates, nudges work by making safer choices easier and more appealing without removing individual freedom. Applying nudge theory to hand safety in Indian workplaces can lead to a transformative cultural shift toward better safety practices.
Understanding Nudge Theory
Nudge theory, popularized by Richard Thaler and Cass Sunstein in their book Nudge: Improving Decisions About Health, Wealth, and Happiness, posits that people often make decisions based on context, habits, and immediate convenience rather than rational analysis. Nudges subtly alter this decision-making context to guide individuals toward better choices.
For example, placing healthier foods at eye level in a cafeteria encourages better eating habits without restricting other options. Similarly, implementing nudges in workplace safety can make protective behaviors more intuitive and automatic for workers.
The State of Hand Safety in India
India’s workforce spans diverse sectors, many of which involve high-risk tasks requiring manual labor. Common hand injuries include:
• Cuts and lacerations from sharp tools or machinery.
• Burns from exposure to chemicals or heat.
• Crush injuries from heavy equipment or falling objects.
• Repetitive strain injuries due to prolonged use of certain tools.
Despite safety guidelines, several barriers hinder adherence:
1. Lack of Awareness: Many workers are unaware of proper hand safety measures or the risks of non-compliance.
2. Cost Constraints: Employers and workers often perceive safety equipment as an added expense.
3. Cultural Factors: A mindset of prioritizing productivity over safety leads to negligence.
4. Inadequate Enforcement: Compliance monitoring is often inconsistent in smaller industries or informal sectors.
Leveraging Nudge Theory for Hand Safety
Nudge theory offers a practical and cost-effective way to overcome these challenges. Below are some strategies to enhance hand safety in Indian workplaces:
1. Redesigning Workspaces and Tools
• Problem: Workers often bypass safety measures because tools are inconvenient or ergonomically unsuitable.
• Nudge Solution:
o Use color-coded tools to differentiate between safe and unsafe options. For instance, mark handles of frequently used tools with bright, contrasting colors to promote proper grip.
o Introduce visually intuitive tool designs, like safety knives with automatically retracting blades.
o Rearrange workspaces to make safety equipment, such as gloves, more accessible than unsafe shortcuts.
2. Promoting the Use of Protective Gear
• Problem: Many workers avoid wearing gloves due to discomfort or the perception that they slow productivity.
• Nudge Solution:
o Create default systems where gloves are provided with tools as a package.
o Personalize protective gear with workers' names or preferred colors to increase attachment and use.
o Introduce small rewards for consistent use of safety gear, such as recognition boards or tokens redeemable for incentives.
3. Behavioral Training Programs
• Problem: Traditional safety training sessions are often seen as monotonous and fail to change behavior.
• Nudge Solution:
o Use gamification to make training interactive and engaging. For example, set up virtual simulations where workers earn points for identifying hazards or practicing safe behavior.
o Incorporate storytelling to make the consequences of neglecting safety more relatable and memorable.
o Display visual cues, such as posters showing common hand injuries and how gloves prevent them, at key locations like tool stations.
4. Simplifying Compliance
• Problem: Complex rules or processes discourage adherence.
• Nudge Solution:
o Use visual reminders such as footprints or hand icons leading to safety stations.
o Install automated dispensers for hand sanitizers or barrier creams near entrances, so workers are reminded to use them.
o Provide step-by-step infographics for using protective gear, ensuring clarity and ease of use.
5. Encouraging Peer Accountability
• Problem: Workers often follow the unsafe practices of colleagues.
• Nudge Solution:
o Foster a buddy system where workers are paired to monitor and encourage each other’s safety habits.
o Publicize safety achievements of teams or individuals, creating a culture of healthy competition.
o Use social proof by displaying statistics or testimonials showing how others in similar roles benefit from safety adherence.
Benefits of Nudge-Based Hand Safety Programs
1. Cost-Effectiveness: Nudges require minimal investment compared to strict enforcement or punitive measures. Simple changes in design and behavior can yield significant safety improvements.
2. Sustainability: Nudges encourage voluntary adoption of safe practices, making them more sustainable than mandates that require constant monitoring.
3. Cultural Shift: By embedding safety into everyday routines, nudges foster a workplace culture where safety becomes second nature.
4. Reduced Injuries: Fewer accidents translate to lower medical costs, less downtime, and higher worker morale.
Real-World Success Stories
Several global examples demonstrate the effectiveness of nudge theory in workplace safety:
• The UK Rail Industry: By using visual cues like green footprints leading to safety stations, compliance with protective gear increased significantly.
• Construction in Singapore: Introducing gloves with ergonomic designs and default distribution policies reduced hand injuries by over 30%.
• Automotive Plants in the US: Placing tools ergonomically and personalizing safety gear fostered greater usage and reduced repetitive strain injuries.
India can adapt these strategies to its unique workforce challenges, leveraging the behavioral insights of nudge theory to create safer workplaces.
Challenges and Considerations
While nudge theory offers immense potential, its success depends on careful implementation:
1. Customization: Nudges must align with cultural and organizational contexts to be effective.
2. Monitoring: While nudges promote voluntary behavior, periodic evaluation ensures their continued effectiveness.
3. Complementary Policies: Nudges should be part of a broader safety strategy that includes education, enforcement, and incentives.
Toward a Safer Future
Applying nudge theory to improve hand safety in Indian workplaces is a transformative approach that balances innovation with practicality. By subtly guiding workers toward safer choices, employers can address the root causes of unsafe practices, reduce injuries, and build a resilient, safety-conscious workforce.
India’s industrial and economic growth relies heavily on its labor force. Protecting workers through modern, behavior-focused strategies like nudge theory is not just an ethical responsibility—it’s a smart investment in the nation's future. With the right interventions, hand safety can move from being an obligation to an ingrained habit, fostering safer, more productive workplaces across the country.