HYDROGEN DETECTION IN GAS TURBINE
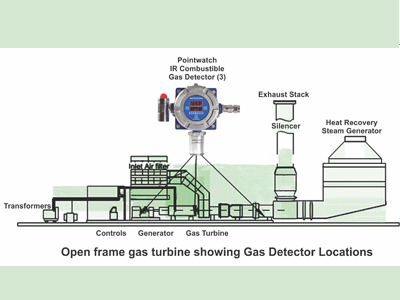
Modern gas turbines are designed to burn light oils (Naphtha) or natural gas. But not only the fuels also the lubricating oils and cooling agents like hydrogen add-up to a high degree of hazard potential. For this reasons, a multiple line of defence has to be established to guarantee protection against fire and explosion risks. Gas detection instruments and optical fire detectors are the central element in the protection systems.
The total market of gas turbines is about 1000 units a year, representing up to 8000-10000 gas detection points. The main producers of turbines are General Electric, Siemens/Westinghouse, Alstom, Caterpillar/Solar Turbines and Mitsubishi
Typical applications:
- ✦ Compressor Stations at Gas Pipelines
- ✦ Oil Production
- ✦ Power Generation
- ✦ Water & Sewage Pumping Stations
- ✦ Oil & Gas Wellhead Re-injection
There are three main areas of risk assessment related to gas detection systems. All different segments require specially matched systems with features optimized for each application
1. Turbine Air Intake
Gas turbines are typically located in areas where large amounts of combustible gases or liquids are stored. They are either used as fuels to feed the turbine or they are part of the application itself as in gas pipeline compressor stations. Leaks in these areas can have disastrous consequences when the supply air of the turbines is already loaded with combustible gases or vapors. There is a genuine risk of pre-ignition of the air/gas mixture in the compressor stage of the turbine or the excess of fuel can result in an uncontrolled over-speed of the turbine. Both situations require immediate shut down of the turbine.
To generate an early warning the intake air has to be controlled for any build-up of hazardous combustible gas concentrations. Infrared optical measurement techniques have proven to be reliable and fast detection systems for this application. The best place to position of the detectors is just outside or in the air intake hoods. Positioning is critical with regard to the high air speed in the ducts. Special care has to be taken to avoid miss readings of gas concentrations related to this mode of operation.
2. Acoustic Turbine Enclosure
The significant noise levels of gas turbines often require an acoustic enclosure. They have to be ventilated to ensure an optimum temperature range of the turbine. Typical operation conditions are 40-60°C. However, under hot environments, near the combustion chamber or under equipment failure conditions the internal temperatures can reach values up to 100 °C. The turbine is feed with high pressure (700 p.s.i. / 50 bar) combustion fuel. Hundreds of connections and the complex distribution system are always a source of potential leakage inside the enclosure. Also the lubrication oil system can spill into the acoustic chamber in case of malfunctions. To prevent the system under these circumstances from a build-up of high concentrations of flammable gases a gas detection system has to be installed.
Most detectors are restricted to upper limits of 65°C as for example optical measurement systems. These set-ups require positioning of the detectors outside the enclosure and extractive sampling systems with additional measurement gas conditioning.
3. Hydrogen Cooling System
The power output rating of all combustion turbines is based on the inlet air temperature. The output capacity of the turbines decreases with an increase in ambient air temperature. Therefore, in hot weather climates or on hot days, cooling of turbine inlet air has been found to be cost-effective for many power plants for boosting power output. Hydrogen-driven heat exchangers are frequently the best choice for removing heat from the high-power generators in this application. Hydrogen has a high heat capacity and, therefore, removes excess heat efficiently. Hydrogen also has a very low viscosity (or windage), thus allowing higher capacity operation of the generators while maintaining efficient cooling.
On the other hand, Hydrogen is known to be a highly combustible gas. Leaks in the closed cooling system cycles can be an additional source of a potential hazard while operating a gas turbine. Catalytic bead detectors or electrochemical sensors are highly sensitive in detecting Hydrogen and can pick up this risk.
Ambetronics offers a complete range of solutions for all safety applications around gas turbines. Catalytic and infrared sensors for combustible gases and electrochemical gas sensors for monitoring of toxic gases and hydrogen are available.
Infrared Point Gas Detectors
Ambetronics IR-5000 Infrared gas detectors has a speed of response of less than 30 seconds, maintenance free operation and self-test functions guarantee reliable warning and a low cost of ownership of the safety equipment.
Duct mounting installations at the air intake points as well as in exhaust ducts of the acoustic chambers belong to the standard portfolio of Ambetronics gas detection equipment. When temperatures above 65°C restrict the direct measurement at the point of hazard with infrared instruments a complete sampling system including measurement gas conditioning can be offered.
Catalytic Bead Detectors
Especially at the measuring points of the internal area of the acoustic chambers, very high temperatures are possible by using the Ambetronics Gas Analyzer system which draw sample gas from the internal area of the chamber and detects any flammable gas present in the area. Pellistors are also the only possibility to detect Hydrogen leaks in the LEL range. While IR detectors are not sensitive to Hydrogen catalytic bead sensors are known to give reliable warnings in the 0-100% LEL range.
Electrochemical Gas Detectors.
Even small leakages of Hydrogen can be detected by electrochemical sensors. This guarantees the earliest warning and the possibility of controlled actions of safety measures to avoid a build-up of hazardous concentrations. Measurement ranges down to 0-500 ppm and even lower alarm settings are possible when using Ambetronics GT-2500 Hydrogen transmitters.
Another source of hazard risks can be an accumulation of toxic gases generated via leaks in the exhaust systems of the turbines. In such cases, toxic Carbon Monoxide concentrations and Oxygen depletion can be measured by electrochemical sensors.
www.ambetronics.com
(This "Article" Published in October 2023 Edition)